Rotary Vane Compressor
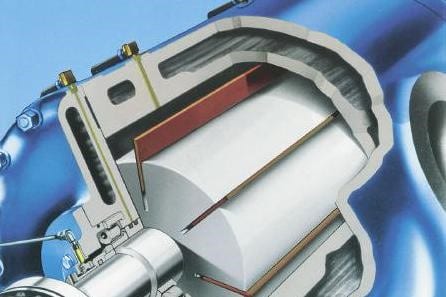
Principle
A single rotor is mounted offset in a cylindrical housing. Slots in the rotor contain vanes, which are thrown against the wall of the housing as it rotates.
Oil is injected into the compression space to lubricate the bearings and vanes. As the rotor is offset, the segments that are created by the vanes vary in size through the cycle, causing the trapped gas to be compressed.
Ports in the housing wall are positioned to let the gas in and out at the points of minimum and maximum pressure. Fully oil flooded versions are also available, with no oil loss to process.
Typical Performance Envelope | ||||||||||||||||||||||||||||
|
||||||||||||||||||||||||||||
Advantages | ||||||||||||||||||||||||||||
|
||||||||||||||||||||||||||||
Disadvantages | ||||||||||||||||||||||||||||
|
||||||||||||||||||||||||||||
Common Applications | ||||||||||||||||||||||||||||